A Comprehensive Guide to PUWER Training: Ensuring Workplace Safety and Compliance
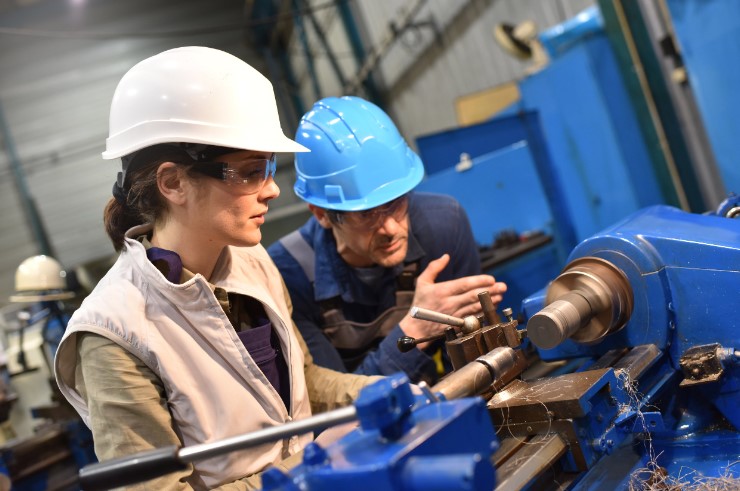
In today’s fast-paced work environments, ensuring the safety and well-being of employees is of utmost importance. Accidents and injuries not only harm individuals but can also have severe consequences for businesses, including financial loss, decreased productivity, and damage to reputation. That’s why implementing robust safety measures and providing comprehensive training is crucial, especially when it comes to the operation and use of work equipment.
This blog post aims to shed light on an essential aspect of workplace safety: PUWER training. PUWER, which stands for the Provision and Use of Work Equipment Regulations, is a set of regulations enforced in the United Kingdom to ensure that work equipment is safe to use, properly maintained, and operated by competent individuals. By adhering to PUWER regulations and investing in comprehensive training programs, organizations can create a culture of safety, reduce accidents, and protect their most valuable asset—their employees.
Throughout this post, we will explore the significance of PUWER training and its impact on workplace safety and compliance. We will delve into the regulations, requirements, and best practices associated with PUWER training, providing you with the knowledge and insights necessary to create a safer work environment. Whether you are an employer, manager, or employee, understanding PUWER training is essential for promoting safety, mitigating risks, and meeting legal obligations.
Let’s embark on this journey to discover the world of puwer training by ST&L, and equip ourselves with the tools and knowledge needed to ensure workplace safety and compliance.
What is PUWER Training?
PUWER training refers to the educational programs and courses designed to familiarize workers with the regulations and requirements outlined in the Provision and Use of Work Equipment Regulations (PUWER). These regulations, enforced in the United Kingdom, aim to ensure that work equipment is safe to use, properly maintained, and operated by competent individuals.
The primary goal of PUWER training is to equip employees with the knowledge and skills necessary to handle work equipment safely and responsibly. By providing comprehensive training, organizations can reduce the risk of accidents, injuries, and potential hazards associated with the use of work equipment.
PUWER training covers various aspects, including understanding the legal obligations outlined in the regulations, conducting thorough risk assessments, implementing effective control measures, and ensuring proper equipment maintenance and inspection. It also includes training on emergency procedures, such as shutdown protocols, evacuation plans, and first aid measures.
Training programs are typically tailored to specific industries and job roles to address the unique challenges and requirements of different work environments. Whether employees work with machinery, tools, vehicles, or other types of work equipment, PUWER training is essential to ensure their competence and safety in performing their tasks.
By participating in PUWER training, employees gain a comprehensive understanding of the regulations, learn to identify and assess potential risks associated with work equipment, and acquire the skills needed to operate and maintain equipment safely. This training empowers employees to contribute to a safer work environment and minimizes the chances of accidents, injuries, and costly disruptions.
In the next section, we will explore the key elements of PUWER regulations and delve deeper into understanding their implications and significance for workplace safety and compliance.
Understanding PUWER Regulations
To comply with PUWER and ensure workplace safety, it is essential to have a solid understanding of the regulations and their implications. Let’s delve into the key components of PUWER and explore how they contribute to maintaining a safe work environment.
- Legal Obligations: PUWER places legal obligations on employers, self-employed individuals, and those in control of work equipment. It requires them to ensure that work equipment is suitable for its intended use, maintained in a safe condition, and inspected regularly. Employers are also responsible for providing adequate training, information, and supervision to employees to ensure their safety.
- Risk Assessments: PUWER emphasizes the importance of conducting thorough risk assessments for work equipment. A risk assessment involves identifying potential hazards, evaluating the level of risk, and implementing control measures to mitigate those risks. Employers must assess the risks associated with the use of work equipment and take appropriate actions to minimize them.
- Equipment Certification: PUWER requires employers to ensure that work equipment meets relevant safety standards. This includes ensuring that equipment is CE marked where required, indicating compliance with European directives. Employers must ensure that the equipment is safe for use, properly maintained, and inspected regularly by competent individuals.
- Inspection and Maintenance: Regular inspections and maintenance play a crucial role in ensuring the ongoing safety of work equipment. PUWER requires employers to establish appropriate inspection schedules, conduct routine maintenance, and promptly address any identified defects or issues. Adequate records of inspections, maintenance activities, and repairs should be maintained.
- Training and Competence: PUWER places an emphasis on providing employees with adequate training and ensuring their competence in operating work equipment safely. Employers should assess the skills and knowledge required for each job role and provide appropriate training to employees. This training should cover equipment operation, maintenance, emergency procedures, and any specific hazards associated with the work environment.
By understanding and complying with PUWER regulations, employers can create a safe work environment, protect their employees, and meet legal requirements. In the next section, we will explore the essential training requirements associated with PUWER and how organizations can ensure their workforce is adequately trained and competent in maintaining workplace safety.
Essential Training Requirements
To ensure workplace safety and compliance with PUWER, organizations must fulfill certain training requirements. By equipping employees with the necessary knowledge and skills, organizations can create a culture of safety and empower individuals to handle work equipment responsibly. Let’s explore the essential training elements associated with PUWER.
- Identifying Training Needs: The first step in developing a comprehensive PUWER training program is identifying the specific training needs of employees. This involves assessing the equipment they work with, their job roles, and any potential risks involved. By understanding the unique requirements of each employee, organizations can tailor their training programs effectively.
- Risk Assessment Techniques: PUWER training should cover effective risk assessment techniques. Employees need to learn how to identify potential hazards associated with work equipment and evaluate the level of risk involved. This includes understanding risk control measures and strategies to mitigate identified risks. By conducting thorough risk assessments, employees can contribute to a safer work environment.
- Equipment Inspection and Maintenance: Training on equipment inspection and maintenance is crucial for maintaining workplace safety. Employees should understand the importance of regular inspections, how to identify defects or issues, and the appropriate steps to take in reporting and addressing them. Proper maintenance procedures and preventive measures should also be emphasized to minimize the risk of equipment failure.
- Emergency Procedures: PUWER training should include instruction on emergency procedures related to work equipment. This encompasses knowledge of shutdown processes, evacuation plans, and first aid measures in case of equipment-related accidents or incidents. Employees should be aware of the steps to take to ensure their safety and the safety of others during emergencies.
- Regular Training Updates: PUWER training is not a one-time event but an ongoing process. It is important to provide regular training updates to employees to keep their knowledge and skills up to date. This can include refresher courses, workshops, or training sessions focused on specific equipment or emerging safety concerns. Regular training updates help reinforce good practices and ensure employees remain competent in their roles.
By addressing these essential training requirements, organizations can foster a culture of safety, empower their employees, and enhance workplace compliance with PUWER regulations. In the next section, we will explore key topics covered in PUWER training, providing further insights into the specific areas that training should focus on.
Key Topics Covered in PUWER Training
PUWER training covers a range of critical topics related to work equipment safety. By addressing these key areas, organizations can ensure that their employees are equipped with the necessary knowledge and skills to operate work equipment safely and comply with regulations. Let’s explore these key topics in detail:
- Risk Assessment: Effective risk assessment is a fundamental aspect of PUWER training. Employees should be trained on how to identify potential hazards associated with work equipment and evaluate the level of risk involved. They should understand the importance of assessing risks before operating equipment and implementing appropriate control measures to mitigate those risks.
- Equipment Certification: PUWER training should cover the importance of equipment certification and compliance with safety standards. Employees should understand the significance of using properly certified equipment that meets the necessary requirements for safe operation. They should be aware of the relevant certifications, markings, and labels that indicate equipment compliance.
- Inspection and Maintenance: Proper inspection and maintenance of work equipment are vital to ensure its ongoing safety. PUWER training should include instruction on inspection techniques, such as visual inspections, functional checks, and testing procedures. Employees should also learn how to recognize signs of equipment wear, damage, or malfunction and understand the importance of reporting and addressing these issues promptly.
- Safe Operation: Employees need to be trained on the safe operation of work equipment. This includes understanding the correct usage, operating procedures, and best practices to minimize the risk of accidents or injuries. Training should cover topics such as machine controls, handling techniques, ergonomic considerations, and safe work practices specific to the equipment they work with.
- Emergency Procedures: PUWER training should address emergency procedures related to work equipment incidents. Employees should be familiar with protocols to follow in case of equipment failures, malfunctions, or accidents. This includes knowledge of shutdown processes, evacuation plans, emergency contact information, and first aid measures to provide immediate assistance if needed.
By covering these key topics in PUWER training, organizations can ensure that their employees have the necessary knowledge and skills to handle work equipment safely and mitigate potential risks. In the next section, we will explore the benefits of PUWER training and the positive impact it can have on workplace safety and compliance.
Benefits of PUWER Training
PUWER training offers numerous benefits for both organizations and employees. By investing in comprehensive training programs that adhere to the Provision and Use of Work Equipment Regulations, organizations can create a safer work environment and foster a culture of safety. Let’s explore the key benefits of PUWER training:
- Enhanced Workplace Safety: The primary benefit of PUWER training is the improvement of workplace safety. By equipping employees with the necessary knowledge and skills, organizations can reduce the risk of accidents, injuries, and occupational hazards. Training empowers employees to identify potential risks, implement control measures, and handle work equipment safely, minimizing the chances of incidents occurring.
- Reduced Accidents and Injuries: PUWER training plays a crucial role in reducing workplace accidents and injuries. Through proper training, employees gain a deeper understanding of the hazards associated with work equipment and learn how to mitigate those risks. By following safe operating procedures and best practices, the likelihood of accidents and injuries is significantly reduced, resulting in a safer work environment for all.
- Compliance with Legal Requirements: PUWER training ensures that organizations comply with the legal obligations outlined in the regulations. By providing comprehensive training, employers demonstrate their commitment to meeting the requirements set forth by PUWER. Compliance with these regulations not only avoids potential penalties and legal consequences but also helps create a workplace culture that values safety and meets the expectations of regulatory authorities.
- Improved Employee Morale and Confidence: Investing in PUWER training demonstrates a commitment to employee well-being and safety. When employees receive thorough training, they feel valued and supported by their organization. This, in turn, boosts morale and confidence, as employees are equipped with the knowledge and skills necessary to perform their tasks safely and effectively. A workforce that feels safe and supported is more likely to be engaged, productive, and loyal.
- Cost Savings: Implementing PUWER training programs can result in cost savings for organizations. By reducing accidents and injuries, organizations avoid associated costs such as medical expenses, compensation claims, and potential legal fees. Moreover, improved workplace safety leads to increased operational efficiency, reduced downtime, and minimized equipment damage or loss, resulting in overall cost savings for the organization.
By prioritizing PUWER training, organizations can create a safer work environment, protect their employees, and reap the benefits of improved compliance, reduced accidents, and increased productivity. In the concluding section, we will summarize the importance of PUWER training and emphasize the need for organizations to prioritize this essential aspect of workplace safety.
Conclusion
PUWER training is a vital component of workplace safety and compliance with the Provision and Use of Work Equipment Regulations. By providing comprehensive training programs that cover key topics such as risk assessment, equipment certification, inspection and maintenance, safe operation, and emergency procedures, organizations can create a safer work environment and protect their employees from potential accidents and injuries.
Through PUWER training, employees gain the necessary knowledge and skills to identify hazards, assess risks, and implement control measures to mitigate potential dangers associated with work equipment. This training not only enhances workplace safety but also demonstrates compliance with legal obligations, leading to a more productive and engaged workforce.
Investing in PUWER training brings multiple benefits, including reduced accidents and injuries, enhanced employee morale and confidence, compliance with regulations, and cost savings. Organizations that prioritize PUWER training prioritize the well-being of their employees and create a culture that values safety.
In conclusion, PUWER training is not just a legal requirement, but a crucial step towards maintaining a safe work environment. By equipping employees with the necessary training, organizations can mitigate risks, protect their employees, and promote a culture of safety. Remember, investing in PUWER training is an investment in the well-being and success of both the organization and its employees.