All-electric investment fast-tracks productivity and raises OEE bar for Hampshire moulder
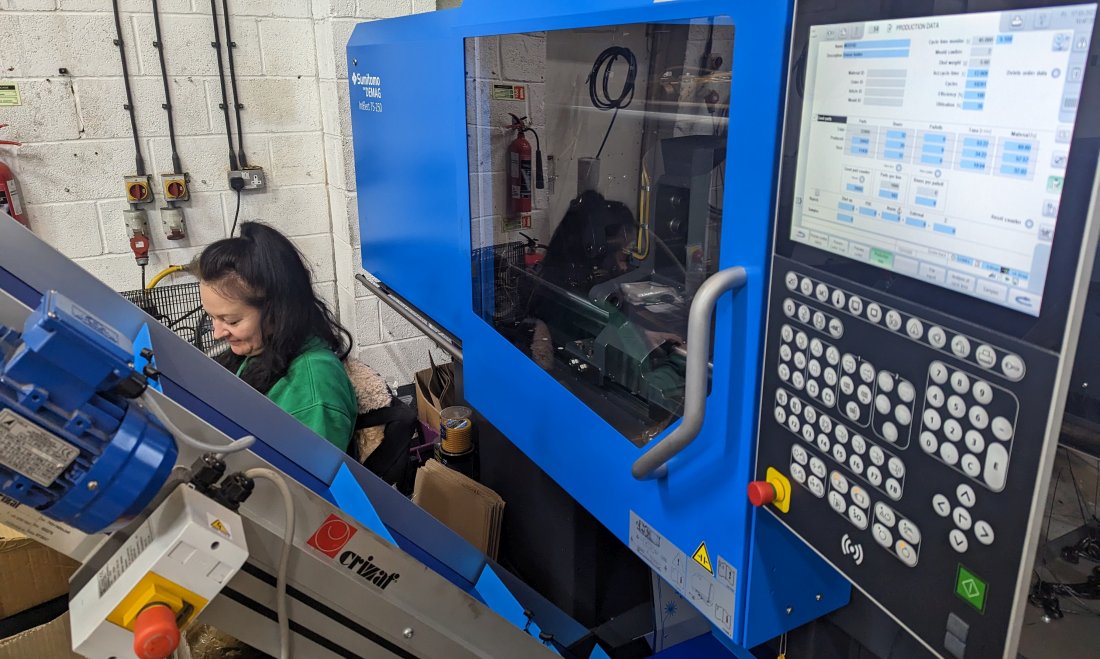
Specialist technological trade moulder D&G Moulding has ramped up productiveness by around 40 for every cent and decreased vitality intake by about 75 for each cent with its latest machine investment – a 75-ton all-electric IntElect from Sumitomo (SHI) Demag.
Specialising in production premium automotive, aerospace, industrial marine and clinical elements in a range of elements, the Alton-dependent moulding business prides by itself on operating a lean, resilient, significant-volume output operation. Like a lot of, the price of residing disaster and electrical power price uncertainty was weighing heavily on the company’s thoughts. Eager to consider measures to protect and long term evidence their company, Controlling Director David Ivey commenced an in depth because of diligence exercising reviewing the power performance of diverse European injection moulding devices.
Narrowing the choice of a equipment replacement to supersede a reputable, but 22-calendar year-aged unsupported hydraulic equipment, David’s remaining financial commitment final decision was influenced by industry colleagues. “More than anything at all, I valued their neutral suggestions. Some persons have been machines suppliers. Other individuals had set up IntElect machines in their output operations. There was resounding affirmation that this all-electric machine delivered on all factors of precision moulding and electrical power effectiveness,” demonstrates David. D&G’s founder was equally fascinated in having obtain to regional support assistance and complex backup.
Theoretical strength comparisons adopted by a tool trial at Sumitomo (SHI) Demag’s Academy in Daventry gave David a ballpark 75 p.c reduction in vitality use when benchmarked from the hydraulic machine getting retired. “As an SME, investing in a new equipment is a big determination. But when spares are no more time getting created for existing machinery, you do reach a tipping point when ongoing upkeep and the likely downtime can undermine productivity and potential viability.”
Even with all the facts at his fingertips, David nonetheless desired strong production information to give assurance and a in-depth OEE and price tag-profit evaluation. The Daventry device demo presented this. Instantly, it disclosed that functioning the similar 8-cavity tool on an IntElect 75-ton was consuming approximately a quarter of the electricity in contrast to their outgoing hydraulic. On top of that, as a consequence of the IntElect’s parallel actions, cycle times were being on common 15 percent quicker.
In a stay output environment, the results have tested to be even additional outstanding. D&G’s experienced operative and device setter Graeme has noticed 20 2nd cycle times minimize to 12.5 seconds, boosting productiveness by up to 40 per cent and expanding D&G’s manufacturing capability. “We are producing close to eight distinct components on the IntElect at this time. On typical, dry cycle time discounts are all over 20 per cent,” exclaims Graeme. As a immediate final result of these findings, the Alton-enterprise is presently weighing up the added benefits of including a bigger tonnage (130 or 180) all-electrical machine to its fleet.
“On leading of the electrical power financial savings, these productiveness enhancements means that we can reliably dedicate to fulfil orders even more quickly for our shoppers,” provides David.
Services gratification
Obtaining served D&G for more than two many years, David is eager not to knock his hydraulic workhorse. On the other hand, the escalating strength expenditures intended that as a ahead wanting company, all-electric powered was the way to go.
Outfitted with activeRemote, David can now also entry specialized backup at the press of a button. With just 4 equipment, acquiring just one out of motion for a working day or additional is his worst nightmare.
“Having this remote diagnostics function, which permits the Sumitomo (SHI) Demag aid staff to dial into the device and take care of queries, has been in particular handy for our setters when receiving common with the IntElect’s new attributes and controls. I particularly recognize knowing that this aspect is separate from the rest of our production method. It is a secure relationship, which provides me self-confidence,” emphasises David.
On leading of put up-installation instruction, David also values owning entry to Sumitomo (SHI) Demag’s IOM3-accredited schooling at the Daventry Academy. A single D&G workforce member has already been signed up to the a few-day Toolsetting Know-how course. A different will soon finish the a few-working day State-of-the-art Injection Moulding (Intention) training course. Both courses characteristic official assessments and give SMEs like D&G with the useful expertise that can be applied back in the place of work to optimise moulding cycles, further more increase OEE and improve productivity.
As a tier two provider to the quality automotive industry, dimensional moulding steadiness is crucial. “Although polypropylene is a somewhat secure material to mould, the IntElect’s immediate drives supply precision and management around the injection force. This is critical for mouldability and ingredient good quality,” states David.
The IntElect equipment, outfitted with activeFlowBalance has once more proved its well worth when moulding large-conclude engineering components. David describes: “Shot-to-shot, the repeatability of the IntElect is outstanding. But when put together with activeFlowBalance on multi-cavity tools, equal soften force is quickly applied in just about every cavity making sure repeatable portion good quality. This element signifies that our machine setters are not owning to continuously reset advanced injection profiles.”
It is this degree of precision moulding and ingredient excellent that is driving OEMs again to sourcing components from the British isles, thinks David. D&G is previously in discussion with yet another community enterprise that’s trying to find to reshore large-volume moulding operate from China to Hampshire. “Until just lately, SMEs like ourselves have been competing with destinations where labour charges are the lowest. Nonetheless, specified that most moulding jobs can be automatic or, like D&G, can run uninterrupted for eight hrs throughout the evening on our new IntElect, labour charges has correctly develop into a moot issue.”
Summing up the biggest problem for all trade, complex and expert moulders, David finishes: “Today’s reality is the value of power is now the only serious thought. In particular with regard to upcoming resilience. It is why D&G has started out the journey with Sumitomo (SHI) Demag to all-electric powered. The effects discuss for them selves.”
Browse additional of our Sustainability articles below