Benefits Of Air Compressors In The Manufacturing Industry
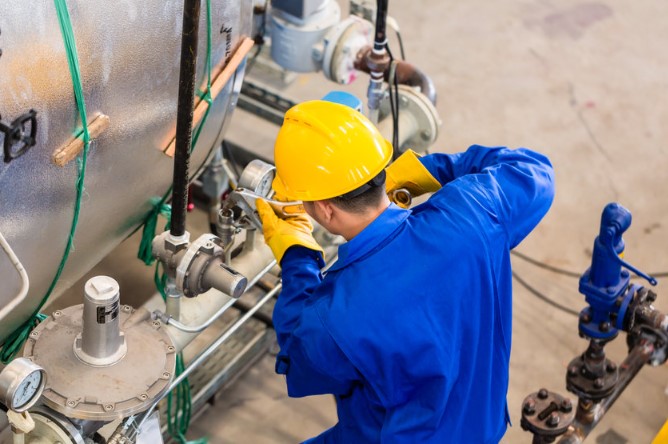
The manufacturing industry, a cornerstone of modern economies, has undergone significant transformations over the decades. From the days of rudimentary hand tools to the current era of advanced machinery, the evolution has been profound. At the heart of this metamorphosis lies the air compressor. This seemingly simple device has not only streamlined operations but has also played a pivotal role in shaping the trajectory of modern manufacturing processes.
Historical Context
The industrial revolution brought with it a plethora of innovations, but few were as transformative as the advent of pneumatic tools. These air-powered marvels, driven by air compressors, signaled a departure from traditional methods. They bridged the gap between labor-intensive manual processes and the dawn of efficient, mechanized manufacturing. This transition not only boosted productivity but also set the stage for the industrial advancements we witness today.
Basic Principles of Air Compressors
At its core, an air compressor is a marvel of engineering. It operates on the principle of converting power, usually from an electric motor, into potential energy stored in pressurized air. This stored energy, when released, performs a multitude of tasks, driving various tools and machinery. The world of air compressors is vast, with each type designed to cater to specific manufacturing needs, be it centrifugal, reciprocating, or rotary screw compressors.
Energy Efficiency
In an age where sustainability is paramount, air compressors emerge as champions of energy efficiency. By design, they optimize power consumption, storing energy during non-peak times and releasing it as required. This cyclical process ensures that industries can operate sustainably, aligning their practices with global green initiatives and reducing their overall energy expenditure.
Enhanced Productivity
The introduction of air compressors in the manufacturing landscape has been synonymous with a surge in productivity. These machines enable faster production cycles, ensuring that manufacturing targets are met with ease. More importantly, they guarantee a consistent output quality. This uniformity ensures that products, irrespective of when they were manufactured, adhere to the same high standards, eliminating discrepancies.
Safety Improvements
Safety in manufacturing units is of paramount importance. Air compressors, with their efficient design, substantially mitigate the risk of machinery overheating. Their predominantly automated nature minimizes the need for human intervention, reducing the chances of human-induced errors and ensuring a safer, more controlled manufacturing environment.
Versatility in Applications
One of the standout features of air compressors is their adaptability. These machines are not bound by the constraints of specific tools or processes. Their inherent versatility ensures they can power a diverse range of tools, from drills to sprayers. This adaptability allows manufacturers to customize their operations, tailoring them to meet the unique demands of their products and markets.
Cost-Effectiveness
While the initial investment in air compressors might seem steep, their long-term benefits are undeniable. These machines are built for durability, ensuring that they serve industries for extended periods. Their efficiency translates to a marked reduction in maintenance and operational costs, ensuring that businesses remain profitable in the long run.
Space Optimization
Urbanization and the resultant space crunch have made compact machinery a necessity. Modern air compressors, with their sleek designs, are tailor-made for urban manufacturing units grappling with space constraints. Their design ensures seamless integration with existing infrastructure, optimizing space and ensuring smooth operations.
Environmental Benefits
In an era where environmental consciousness is at the forefront, air compressors are a boon. Their design inherently reduces waste, ensuring that manufacturing processes have a minimal environmental impact. By reducing a company’s carbon footprint and promoting eco-friendly manufacturing practices, air compressors align industries with global sustainability goals.
Innovation and Technological Advancements
The realm of air compressors is not static. Continuous innovations, coupled with technological advancements, have ensured that these machines evolve. The integration of air compressors with the Internet of Things (IoT) and smart manufacturing practices is a testament to their adaptability. Furthermore, the advent of predictive maintenance, powered by Artificial Intelligence, augments their efficiency, preempting issues before they escalate.
Operational Reliability
Reliability in manufacturing is non-negotiable. Air compressors, known for their consistent pressure delivery, are stalwarts of reliability. This consistency ensures that operations run smoothly, with reduced downtime, ensuring that production targets are consistently met.
Noise Reduction
A conducive work environment is crucial for worker productivity and well-being. Modern air compressors, with their enhanced designs, operate at reduced noise levels. This quiet operation not only ensures compliance with global noise standards but also fosters a healthier workplace environment.
Ease of Maintenance
The modern-day air compressor is a culmination of years of research and feedback. These machines come equipped with user-friendly interfaces, ensuring that even the most complex tasks are straightforward. Furthermore, the global presence of expert services ensures that maintenance (Control Gear’s premium service), when required, is prompt and efficient.
Global Trends and Market Analysis
The global demand for air compressors is reflective of their indispensability. As manufacturing hubs across regions continue to expand, the reliance on these machines is evident. The growth trajectory of the air compressor market, coupled with regional nuances, offers fascinating insights into their global appeal.
Challenges and Solutions
No machine is without its challenges, and air compressors are no exception. However, what sets them apart is the industry’s proactive approach to addressing these challenges. Continuous research and innovations ensure that limitations are not only identified but also addressed, paving the way for even more efficient and effective models.
Case Studies
The global manufacturing landscape is dotted with success stories, many of which owe their achievements to air compressors. These narratives, from leading manufacturers, offer a treasure trove of lessons. From best practices to innovative solutions, these case studies serve as a guide for industries looking to optimize their operations.
Future Prospects
The future of air compressors is as promising as their illustrious past. With research and development in full swing, the next generation of air compressors is on the horizon. Their potential impact, especially on emerging manufacturing sectors, is immense, making them a focal point of industrial evolution.
Conclusion
In conclusion, air compressors, with their myriad benefits and adaptability, have etched their place in the annals of manufacturing history. Their role, far from being static, continues to evolve, promising a brighter, more efficient future for the global manufacturing industry.