How to Pick High-Quality Sprockets for Your Machines
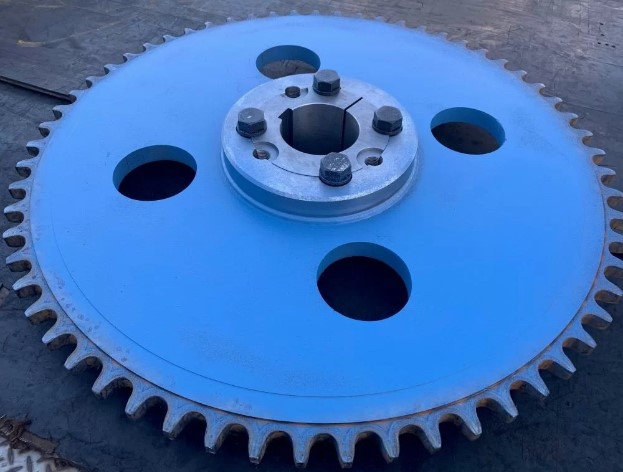
The performance of your manufacturing systems and machines impacts your production and productivity. Whether in the textile, food processing, mining, chemical, or aerospace industry, you must ensure your mechanical, agricultural, or transmission systems run optimally.
The sprocket is a crucial part of these systems. It works with rollers and chains for seamless machine movement by transmitting rotary motion between two shafts where gears are not helpful. Sprockets are available in different types to suit different hub styles in your application.
You must pick high-quality sprockets that suit your machine’s specifications to ensure ample performance. Here are the factors to consider.
1. Material
Sprockets can be made from different materials to suit the intended use, including 45# steel, aluminium (6061 and 7075), 40Mn and 45Mn steel, and stainless steel (201, 304, and 316). The suitable material depends on factors like tension, speed, environment, etc.
The 45# steel is the most commonly used material because it meets the sprocket’s use conditions. It’s cost-effective and ideal for low-speed operations. 304 stainless steel is the preferred option because of its corrosion resistance properties.
2. Type
You should work with professionals to ensure you have the right sprocket type for your machine or process. Different types include idler, steel-split, bushing type, roller chain, single-pitch, drum, and double-pitch. Other options include segmented, soft teeth, welded hub, pilot bore, etc.
For instance, roller chain sprockets are ideal for commercial and industrial applications, such as robotics, conveyors, industrial drives, etc. Drum sprockets are the perfect picks for drag applications, while steel-split sprockets are suitable for chain systems that are difficult to access.
3. Diameter
When replacing your sprockets, it’s crucial to know the correct diameter. This entails understanding the diameter of the sprocket’s pitch, hub, and calliper. The pitch diameter is essential to ensure your selected sprockets fit your chain.
On the other hand, the hub diameter is the outside length of the hub, while the calliper diameter is the length between two opposing tooth valleys. For a perfect fit, the replacement should have the same configurations and size as the worn-out sprocket.
4. Strands
Strands are the rows of teeth along the sprocket’s perimeter. Sprockets are available in single, double, and triple strands, offering different options to suit the type of chains in your machine.
Single-strand sprockets are the most common, but multi-strand sprockets are preferred in applications that demand greater power and torque. Knowing the number of teeth on your sprocket ensures your pick suits your application. For instance, tooth counts of 30 or less usually use double-pitch chains.
Pick the Right Sprockets
For efficient and seamless operation of your agricultural, power transmission or conveyor systems, it’s vital to pay attention to the type of sprockets you use. Be sure to look at your sprocket configurations, coatings, and materials to pick one that suits your application.
You can get one from stock or choose a unique custom option. If you’re looking for high-quality sprockets for transmission, conveyor, or specialised manufacturing, be sure to work with a professional workshop to get an option with the correct configurations.