Manufacturing a cleaner future | MIT News
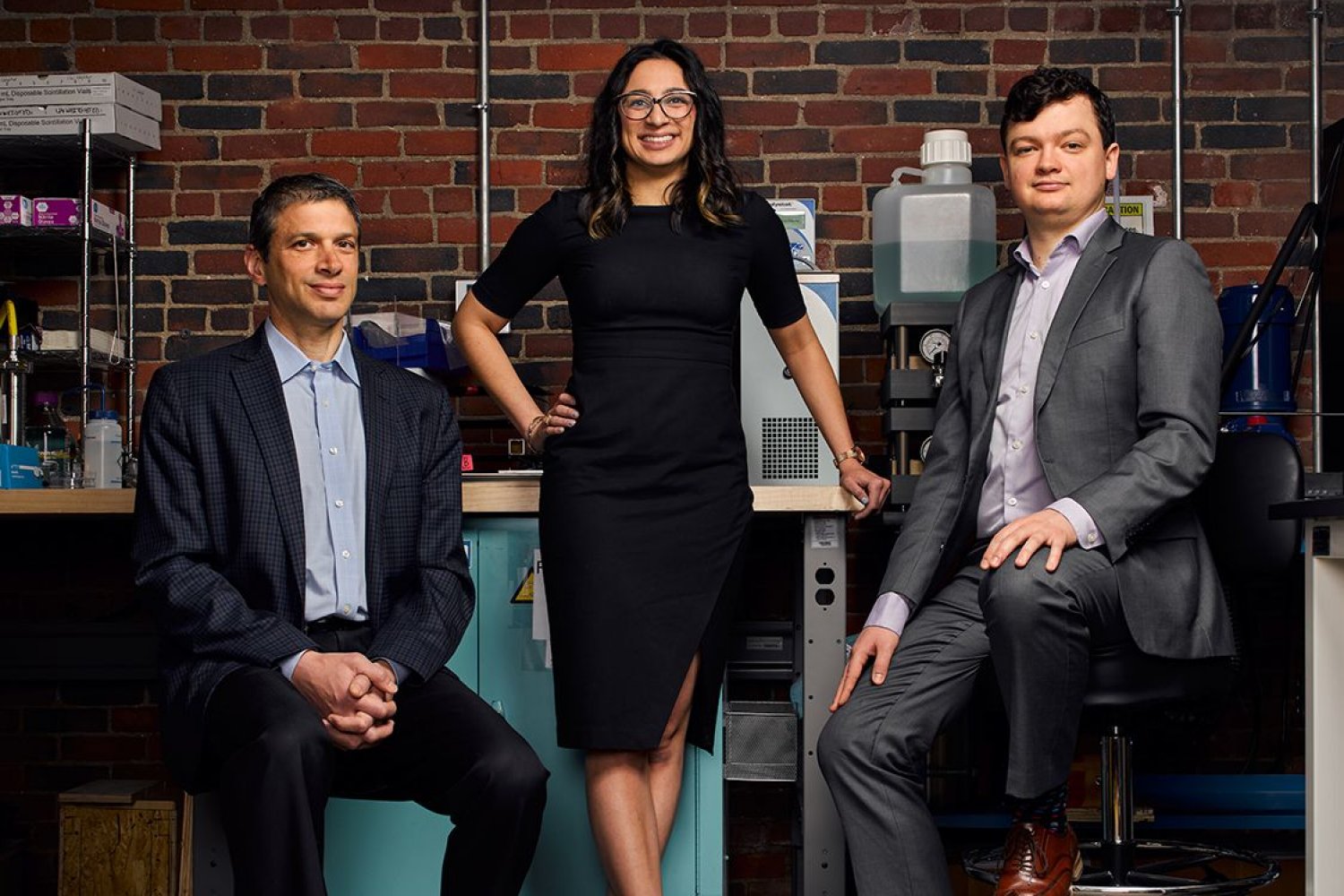
Production had a massive summer time. The CHIPS and Science Act, signed into regulation in August, represents a enormous financial investment in U.S. domestic production. The act aims to significantly broaden the U.S. semiconductor industry, fortify source chains, and commit in R&D for new technological breakthroughs. In accordance to John Hart, professor of mechanical engineering and director of the Laboratory for Production and Productiveness at MIT, the CHIPS Act is just the most recent instance of drastically elevated desire in production in latest years.
“You have multiple forces operating alongside one another: reflections from the pandemic’s influence on source chains, the geopolitical predicament all-around the earth, and the urgency and significance of sustainability,” claims Hart. “This has now aligned incentives among the federal government, market, and the expense neighborhood to accelerate innovation in producing and industrial technological innovation.”
Hand-in-hand with this amplified aim on producing is a require to prioritize sustainability.
Approximately a person-quarter of greenhouse gasoline emissions arrived from marketplace and manufacturing in 2020. Factories and crops can also deplete regional h2o reserves and deliver huge amounts of waste, some of which can be poisonous.
To handle these troubles and drive the transition to a low-carbon economic climate, new goods and industrial procedures have to be formulated together with sustainable production systems. Hart sees mechanical engineers as taking part in a vital function in this changeover.
“Mechanical engineers can uniquely solve crucial troubles that require future-era components systems, and know how to provide their methods to scale,” claims Hart.
Many rapidly-increasing corporations founded by college and alumni from MIT’s Section of Mechanical Engineering give answers for manufacturing’s environmental difficulty, paving the route for a much more sustainable upcoming.
Gradiant: Cleantech water methods
Producing involves water, and lots of it. A medium-sized semiconductor fabrication plant employs upward of 10 million gallons of drinking water a day. In a entire world more and more plagued by droughts, this dependence on water poses a important problem.
Gradiant presents a solution to this h2o problem. Co-established by Anurag Bajpayee SM ’08, PhD ’12 and Prakash Govindan PhD ’12, the organization is a pioneer in sustainable — or “cleantech” — drinking water jobs.
As doctoral students in the Rohsenow Kendall Warmth Transfer Laboratory, Bajpayee and Govindan shared a pragmatism and penchant for motion. They both labored on desalination investigate — Bajpayee with Professor Gang Chen and Govindan with Professor John Lienhard.
Motivated by a childhood used in the course of a intense drought in Chennai, India, Govindan created for his PhD a humidification-dehumidification technologies that mimicked all-natural rainfall cycles. It was with this piece of engineering, which they named Provider Fuel Extraction (CGE), that the duo launched Gradiant in 2013.
The vital to CGE lies in a proprietary algorithm that accounts for variability in the good quality and amount in wastewater feed. At the heart of the algorithm is a nondimensional amount, which Govindan proposes a person working day be named the “Lienhard Quantity,” just after his doctoral advisor.
“When the h2o high quality varies in the process, our technology immediately sends a sign to motors in just the plant to change the stream fees to bring back again the nondimensional variety to a value of a person. After it is introduced back to a price of just one, you are functioning in ideal issue,” points out Govindan, who serves as main functioning officer of Gradiant.
This procedure can deal with and clear the wastewater made by a manufacturing plant for reuse, eventually conserving tens of millions of gallons of drinking water every 12 months.
As the enterprise has developed, the Gradiant team has added new technologies to their arsenal, which includes Selective Contaminant Extraction, a price tag-effective approach that eliminates only distinct contaminants, and a brine-concentration method known as Counter-Circulation Reverse Osmosis. They now offer you a comprehensive technological innovation stack of drinking water and wastewater cure options to consumers in industries like prescription drugs, strength, mining, food items and beverage, and the ever-expanding semiconductor market.
“We are an end-to-conclusion h2o methods supplier. We have a portfolio of proprietary technologies and will select and opt for from our ‘quiver’ depending on a customer’s desires,” claims Bajpayee, who serves as CEO of Gradiant. “Customers look at us as their water husband or wife. We can take care of their water dilemma finish-to-stop so they can focus on their core company.”
Gradiant has observed explosive progress in excess of the past decade. With 450 h2o and wastewater treatment method plants designed to date, they deal with the equal of 5 million households’ worth of water every single day. New acquisitions noticed their total workers rise to earlier mentioned 500.
The variety of Gradiant’s solutions is reflected in their customers, who contain Pfizer, AB InBev, and Coca-Cola. They also count semiconductor giants like Micron Technology, GlobalFoundries, Intel, and TSMC between their consumers.
“Over the last several a long time, we have definitely formulated our abilities and track record serving semiconductor wastewater and semiconductor ultrapure h2o,” says Bajpayee.
Semiconductor manufacturers need ultrapure water for fabrication. Not like drinking h2o, which has a whole dissolved solids vary in the parts per million, h2o utilised to manufacture microchips has a selection in the areas for each billion or quadrillion.
Now, the normal recycling fee at semiconductor fabrication vegetation — or fabs — in Singapore is only 43 p.c. Applying Gradiant’s systems, these fabs can recycle 98-99 percent of the 10 million gallons of drinking water they have to have day-to-day. This reused water is pure plenty of to be put again into the manufacturing system.
“What we’ve finished is removed the discharge of this contaminated drinking water and just about eradicated the dependence of the semiconductor fab on the community drinking water supply,” adds Bajpayee.
With new polices staying launched, tension is raising for fabs to increase their h2o use, creating sustainability even a lot more important to brand name house owners and their stakeholders.
As the domestic semiconductor business expands in mild of the CHIPS and Science Act, Gradiant sees an prospect to bring their semiconductor water treatment method technologies to a lot more factories in the United States.
By way of Separations: Economical chemical filtration
Like Bajpayee and Govindan, Shreya Dave ’09, SM ’12, PhD ’16 centered on desalination for her doctoral thesis. Below the steering of her advisor Jeffrey Grossman, professor of resources science and engineering, Dave built a membrane that could enable additional economical and cheaper desalination.
A comprehensive price and market place assessment introduced Dave to the conclusion that the desalination membrane she made would not make it to commercialization.
“The present-day systems are just actually excellent at what they do. They are small-cost, mass produced, and they worked. There was no home in the sector for our technologies,” says Dave.
Shortly just after defending her thesis, she read through a commentary short article in the journal Mother nature that transformed every little thing. The posting outlined a difficulty. Chemical separations that are central to numerous production procedures have to have a enormous quantity of electrical power. Business essential much more effective and much less expensive membranes. Dave assumed she may possibly have a resolution.
After analyzing there was an financial opportunity, Dave, Grossman, and Brent Keller PhD ’16 launched Through Separations in 2017. Shortly thereafter, they ended up decided on as a person of the 1st corporations to get funding from MIT’s undertaking company, The Engine.
At the moment, industrial filtration is accomplished by heating chemical compounds at incredibly higher temperatures to individual compounds. Dave likens it to producing pasta by boiling all of the h2o off till it evaporates and all you are left with is the pasta noodles. In production, this process of chemical separation is particularly energy-intense and inefficient.
By way of Separations has made the chemical equal of a “pasta strainer.” Relatively than applying heat to different, their membranes “strain” chemical compounds. This technique of chemical filtration uses 90 per cent considerably less energy than normal procedures.
Although most membranes are built of polymers, By using Separations’ membranes are produced with graphene oxide, which can stand up to substantial temperatures and severe circumstances. The membrane is calibrated to the customer’s desires by altering the pore sizing and tuning the area chemistry.
At this time, Dave and her team are focusing on the pulp and paper marketplace as their beachhead market place. They have designed a program that helps make the restoration of a substance recognized as “black liquor” much more electrical power productive.
“When tree results in being paper, only one particular-third of the biomass is made use of for the paper. Currently the most beneficial use for the remaining two-thirds not needed for paper is to just take it from a very dilute stream to a really concentrated stream using evaporators by boiling off the h2o,” says Dave.
This black liquor is then burned. Most of the resulting vitality is employed to energy the filtration course of action.
“This shut-loop technique accounts for an tremendous amount of vitality usage in the U.S. We can make that system 84 per cent much more successful by putting the ‘pasta strainer’ in front of the boiler,” adds Dave.
VulcanForms: Additive producing at industrial scale
The initially semester John Hart taught at MIT was a fruitful one particular. He taught a course on 3D printing, broadly recognized as additive production (AM). While it wasn’t his primary study concentrate at the time, he located the subject matter interesting. So did several of the learners in the class, such as Martin Feldmann MEng ’14.
After graduating with his MEng in state-of-the-art producing, Feldmann joined Hart’s research team complete time. There, they bonded around their shared desire in AM. They saw an opportunity to innovate with an founded metal AM technology, recognized as laser powder mattress fusion, and came up with a principle to notice steel AM at an industrial scale.
The pair co-established VulcanForms in 2015.
“We have formulated a device architecture for steel AM that can make pieces with exceptional good quality and productiveness,” suggests Hart. “And, we have built-in our devices in a completely digital production program, combining AM, postprocessing, and precision machining.”
Contrary to other businesses that promote 3D printers for other individuals to create sections, VulcanForms tends to make and sells pieces for their clients employing their fleet of industrial equipment. VulcanForms has grown to nearly 400 workforce. Final 12 months, the workforce opened their first production factory, recognised as “VulcanOne,” in Devens, Massachusetts.
The high-quality and precision with which VulcanForms produces parts is crucial for solutions like clinical implants, warmth exchangers, and plane engines. Their equipment can print layers of metal thinner than a human hair.
“We’re generating components that are difficult, or in some cases difficult to manufacture otherwise,” provides Hart, who sits on the company’s board of administrators.
The systems produced at VulcanForms may well enable lead to a extra sustainable way to manufacture sections and products, each instantly via the additive approach and indirectly by way of extra economical, agile supply chains.
One particular way that VulcanForms, and AM in typical, encourages sustainability is by materials discounts.
A lot of of the components VulcanForms takes advantage of, such as titanium alloys, demand a great offer of energy to produce. When titanium parts are 3D-printed, significantly a lot less of the content is utilized than in a classic machining course of action. This materials efficiency is where by Hart sees AM producing a huge impression in terms of electrical power cost savings.
Hart also details out that AM can speed up innovation in clean up vitality technologies, ranging from more productive jet engines to potential fusion reactors.
“Companies looking for to de-hazard and scale clear strength technologies need know-how and obtain to sophisticated production capacity, and industrial additive manufacturing is transformative in this regard,” Hart adds.
LiquiGlide: Lowering squander by eliminating friction
There is an not likely perpetrator when it will come to waste in manufacturing and buyer merchandise: friction. Kripa Varanasi, professor of mechanical engineering, and the team at LiquiGlide are on a mission to generate a frictionless foreseeable future, and substantially lower squander in the process.
Started in 2012 by Varanasi and alum David Smith SM ’11, LiquiGlide types custom coatings that enable liquids to “glide” on surfaces. Each and every past drop of a solution can be applied, irrespective of whether it’s being squeezed out of a tube of toothpaste or drained from a 500-liter tank at a manufacturing plant. Earning containers frictionless considerably minimizes wasted item, and eradicates the will need to clean up a container before recycling or reusing.
Because launching, the firm has found great success in shopper products and solutions. Client Colgate utilized LiquiGlide’s technologies in the style and design of the Colgate Elixir toothpaste bottle, which has been honored with quite a few marketplace awards for style and design. In a collaboration with globe- renowned designer Yves Béhar, LiquiGlide is implementing their technological innovation to natural beauty and own care merchandise packaging. In the meantime, the U.S. Food items and Drug Administration has granted them a Unit Grasp Submitting, opening up chances for the know-how to be utilized in medical gadgets, drug delivery, and biopharmaceuticals.
In 2016, the corporation formulated a program to make production containers frictionless. Named CleanTanX, the technologies is used to take care of the surfaces of tanks, funnels, and hoppers, blocking materials from sticking to the side. The procedure can decrease product squander by up to 99 percent.
“This could definitely improve the activity. It saves squandered products, lessens wastewater generated from cleansing tanks, and can enable make the manufacturing process zero-waste,” says Varanasi, who serves as chair at LiquiGlide.
LiquiGlide works by generating a coating built of a textured solid and liquid lubricant on the container surface area. When applied to a container, the lubricant continues to be infused within the texture. Capillary forces stabilize and allow for the liquid to unfold on the surface area, developing a continually lubricated surface that any viscous substance can slide proper down. The firm employs a thermodynamic algorithm to decide the combos of secure solids and liquids dependent on the product, whether it’s toothpaste or paint.
The firm has created a robotic spraying technique that can handle substantial vats and tanks at producing crops on internet site. In addition to preserving organizations millions of dollars in wasted products, LiquiGlide dramatically lowers the quantity of drinking water essential to routinely thoroughly clean these containers, which generally have solution caught to the sides.
“Normally when you empty every little thing out of a tank, you nonetheless have residue that needs to be cleaned with a large total of h2o. In agrochemicals, for case in point, there are strict rules about how to deal with the resulting wastewater, which is harmful. All of that can be eliminated with LiquiGlide,” suggests Varanasi.
When the closure of numerous manufacturing services early in the pandemic slowed down the rollout of CleanTanX pilots at crops, items have picked up in the latest months. As production ramps up equally globally and domestically, Varanasi sees a growing need to have for LiquiGlide’s technologies, specifically for liquids like semiconductor slurry.
Firms like Gradiant, By way of Separations, VulcanForms, and LiquiGlide display that an enlargement in manufacturing industries does not will need to appear at a steep environmental charge. It is possible for producing to be scaled up in a sustainable way.
“Manufacturing has normally been the backbone of what we do as mechanical engineers. At MIT in particular, there is generally a drive to make producing sustainable,” states Evelyn Wang, Ford Professor of Engineering and previous head of the Department of Mechanical Engineering. “It’s amazing to see how startups that have an origin in our section are looking at each individual part of the producing process and figuring out how to make improvements to it for the overall health of our earth.”
As legislation like the CHIPS and Science Act fuels development in production, there will be an amplified will need for startups and providers that develop methods to mitigate the environmental impact, bringing us nearer to a extra sustainable foreseeable future.