Identifying Critical Manufacturing Assets | Supply and Demand Chain Executive
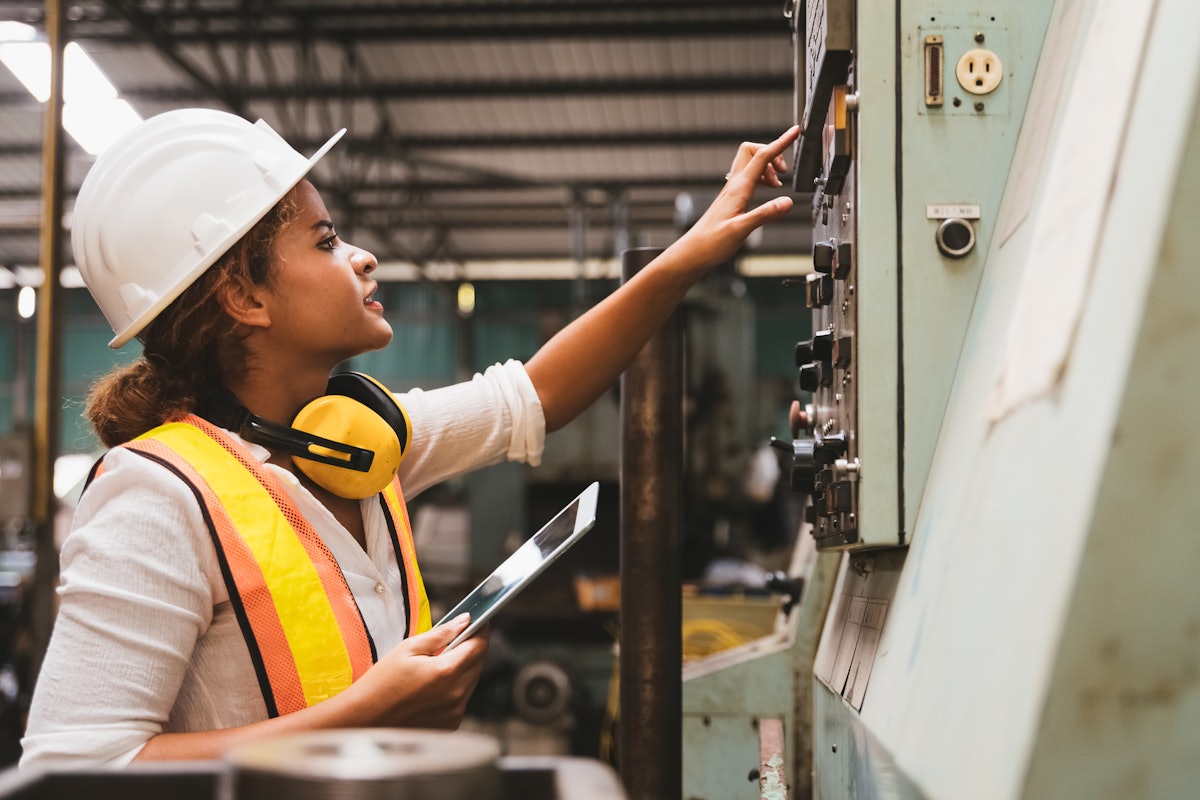

Shutter B/stock.adobe.com
Providers all-around the globe are expanding shelling out on provide chain innovation to successfully navigate pandemic-period disruptions from shortages to the Fantastic Resignation. For the producing market, clogged source chains restrict the circulation of critical spare areas and equipment into manufacturing amenities. With for a longer time direct situations and minimal means coupled with record purchaser demand from customers, producers must navigate the stress to thrust extra goods out when acquiring fewer sources in by optimizing their routine maintenance and dependability plans to maintain the best amount of productivity attainable.
But a lot of businesses today nonetheless are inclined to respond to provide chain disruption by panic-acquiring, stockpiling inventory they may perhaps or may well not need to preserve production strains operating in the potential. Although it could possibly supply some peace of mind to nervous manufacturing industry experts, this solution also results in inventories stuffed with unnecessary inventory, improved overhead expenses, and even better tax costs owing to retaining tangible assets.
As a substitute, brands need to evaluate and determine the relative criticality of their assets and get every single doable move to protect and maintain the most crucial equipment. With a thorough knowing of asset criticality, they can minimize squandered capital in two critical strategies: by not overbuying spare areas and by possessing the appropriate components on hand to prevent significant failures and lengthy downtimes.
Asset criticality assessments for optimizing stock
The purpose of the asset criticality assessment is to uncover data to advise strategic conclusions for producing servicing and stock. With a criticality rating tied to each equipment, suppliers gain a superior thought of which equipment they should devote in monitoring continuously.
By checking the machine health of vital belongings in true time, companies will know in progress when machines are probable to fail and what parts they’ll want on hand to prevent downtime. Equally significant, they’ll identify non-critical property for which they really don’t need to have spare areas stock, enabling decrease overhead charges.
When determining the criticality of equipment, producers have to search for the property that would shut down the output line in the party of failure. These are the vital parts of machines and exactly where organizations will want to invest system and dollars. Devices that is not critical for operating the line or that brands could uncover uncomplicated workarounds to proceed functions is non-significant.
Adapting producing upkeep and trustworthiness practices
Following distinguishing essential from non-essential tools, producers will have to change maintenance and reliability practices to assure sustained efficiency. Begin with 3 critical ways:
1. Watch the suitable products continually.
When equipment health and fitness sensors accumulate and report constantly on the equipment to which they are assigned, maintenance professionals know which equipment need interest and when extensive right before machine failure. But carrying out servicing on non-vital belongings will be an inefficient use of labor that would be more beneficial expended on significant gear.
In addition, continuous facts assortment can be a pricy expense with minimal ROI if sensors are not strategically placed. The moment you’ve identified your most critical assets, adjust your monitoring approach accordingly to allocate costly sensors only to output-vital products.
2. End stockpiling pointless inventory.
Numerous organizations are at this time overbuying components to circumvent equipment downtime thanks to components shortages, but this is an costly and inefficient approach. For a person, it exacerbates the shortages as businesses get out useful resource stock, potentially inflating prices for long term purchases.
One more immediate challenge is that holding additional, unused parts in storage just provides to a listing of taxable assets, which can develop into a substantial cost for manufacturing providers. Alternatively of panic-getting elements, use data from continual checking of essential assets to predict when machines will require repairs with lots of lead time, and prioritize your sections stock based mostly on criticality scores.
3. Avoid excessive preventive maintenance.
Specialists are likely to accomplish servicing on set schedules. For instance, if the failure rate of sure areas exhibits bearings commonly are unsuccessful following six months, specialists replace these elements in advance to protect against the failure — each individual five months, in this case in point.
This may be a much more specific technique than monitoring all devices at all situations or stocking up on replacement elements for every asset, but it can nonetheless be wasteful if businesses put a good deal of capital into pointless repairs. Rather, insights from the steady monitoring of vital products can help companies enhance inventory and labor by pinpointing not only when equipment are probable to are unsuccessful, but also what maintenance groups ought to do to protect against it.
With right asset criticality assessment and strategic continuous checking, suppliers can predict required repairs, enabling more time lead times for securing areas and generating information-pushed conclusions for stock and labor allocation. It’s the wise way to continue to keep operations resilient, preserve production lines functioning, and restrict charges well into the future, no make a difference what unexpected disruptions could come.