Metal Working Lathes
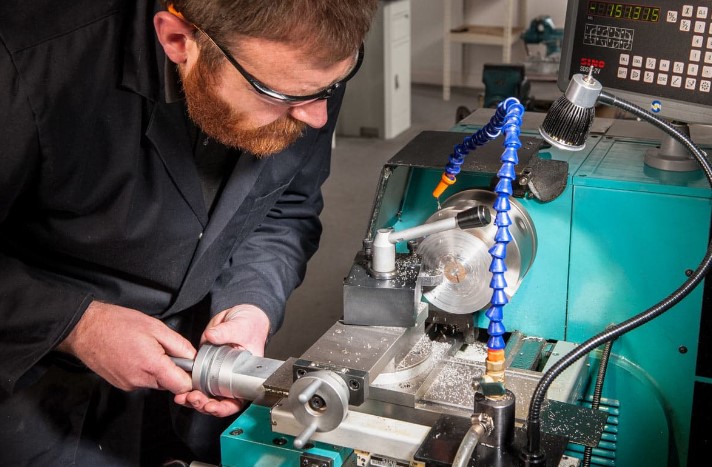
Metal working lathes are indispensable tools in the world of manufacturing and machining. They have played a crucial role in shaping raw materials into intricate components, contributing to the advancement of various Industrial Metals. In this article, we’ll delve into the fascinating realm of metal lathes, exploring their history, types, key components, and applications. Whether you’re a seasoned machinist or a curious enthusiast, this guide will provide valuable insights into the world of metal turning.
History and Evolution of Metal Lathes
The journey of metal lathes dates back centuries, with each era contributing to their evolution. From manual hand-cranked lathes to today’s computer numerical control (CNC) machines, the metamorphosis of metal lathes mirrors the progress of manufacturing itself.
Types of Metal Working Lathes
Engine Lathes
Engine lathes, known for their versatility, are the most common type. They serve a wide range of applications, making them the go-to choice for many machinists.
Turret Lathes
Turret lathes, designed for mass production, feature a rotating turret holding multiple cutting tools. This design allows for quick tool changes, optimizing efficiency.
Special Purpose Lathes
Special purpose lathes cater to specific tasks, such as thread cutting or knurling. While less versatile, they excel in their designated applications.
Key Components of a Metal Lathe
Understanding the anatomy of a metal lathe is crucial for efficient operation.
Bed and Frame
The bed provides a stable platform, while the frame supports various components, ensuring rigidity during machining.
Headstock
The headstock houses the spindle and motor, determining the lathe’s speed capabilities.
Tailstock
The tailstock supports the other end of the workpiece, providing stability during machining.
Carriage
The carriage moves along the bed, holding the cutting tools and facilitating precise metal removal.
Choosing the Right Metal Lathe for Your Needs
Selecting the appropriate Metal working lathes involves considering several factors.
Size and Capacity
The size of the lathe should match the dimensions of your workpieces, ensuring optimal results.
Speed and Power
Different projects require varying speeds and power, so understanding these specifications is crucial for success.
Features and Accessories
Evaluate the available features and accessories, such as digital readouts or tool holders, to enhance your machining experience.
Safety Measures in Metal Turning
Ensuring safety in metal turning is paramount to preventing accidents and injuries.
Protective Gear
Wearing appropriate protective gear, including safety glasses and gloves, is essential.
Proper Training and Education
Proper training in lathe operation and safety protocols is indispensable for anyone using metal lathes.
Machine Maintenance
Regular maintenance, including checking for loose components and lubricating moving parts, is key to preventing malfunctions.
Basic Metal Turning Techniques
Metal turning involves several fundamental techniques.
Facing
Facing is the process of removing material from the end of a workpiece to create a smooth, flat surface.
Turning
Turning is the most common technique, shaping the workpiece as it rotates on the lathe.
Drilling
Drilling creates holes in the workpiece using specialized tools attached to the lathe.
Boring
Boring enlarges existing holes or refines their dimensions.
Advanced Metal Turning Applications
As proficiency grows, machinists can explore advanced applications.
Thread Cutting
Thread cutting allows for the creation of threaded surfaces on cylindrical workpieces.
Knurling
Knurling imparts a textured pattern onto the surface of a workpiece for enhanced grip or aesthetics.
Taper Turning
Taper turning involves gradually reducing the diameter of a cylindrical workpiece.
Tips for Maintenance and Longevity of Metal Lathes
Maintaining your metal lathe is crucial for longevity and consistent performance.
Regular Cleaning and Lubrication
Dust and debris can accumulate, affecting the lathe’s performance. Regular cleaning and lubrication mitigate these issues.
Checking for Wear and Tear
Periodically inspect components for signs of wear and tear, replacing or repairing as needed to prevent further damage.
Notable Innovations in Metal Lathe Technology
The world of metal lathes continues to evolve, incorporating cutting-edge technologies.
CNC Metal Lathes
Computer numerical control (CNC) technology has revolutionized metal turning, offering precision and automation.
Smart Lathe Features
Modern lathes come equipped with smart features, such as remote monitoring and diagnostics, enhancing efficiency and ease of use.
Applications of Metal Working Lathes Across Industries
Metal lathes find applications in diverse industries, from automotive to aerospace, showcasing their versatility.
Challenges and Solutions in Metal Turning
Despite their efficiency, metal lathes pose challenges, including tool wear and material inconsistencies.
Future Trends in Metal Lathe Technology
The future promises exciting advancements in metal lathe technology, with a focus on automation, AI integration, and eco-friendly practices.
Conclusion
In conclusion, metal working lathes are foundational tools that have stood the test of time, continuously adapting to the changing landscape of manufacturing. From their humble beginnings to the era of smart lathes, these machines have shaped the world around us. Whether you’re a hobbyist or a professional, understanding the intricacies of metal lathes opens up a world of possibilities in precision machining.
FAQs (Frequently Asked Questions)
- Q: What safety precautions should I take when using a metal lathe?
- A: Always wear protective gear, undergo proper training, and regularly maintain your lathe to ensure safe operation.
- Q: Can a beginner use a metal lathe for DIY projects?
- A: Yes, with proper training and guidance, beginners can use metal lathes for various DIY projects.
- Q: What are the key differences between engine lathes and turret lathes?
- A: Engine lathes are versatile, while turret lathes are designed for mass production with quick tool-changing capabilities.
- Q: How often should I lubricate my metal lathe?
- A: Regularly lubricate your lathe as per the manufacturer’s recommendations to prevent wear and ensure smooth operation.
-
Q: Are there eco-friendly practices in metal lathe technology?
- A: Emerging trends focus on eco-friendly practices, with innovations in energy-efficient and sustainable metal lathe designs.