Plastic Fabrication Services: Everything You Need to Know
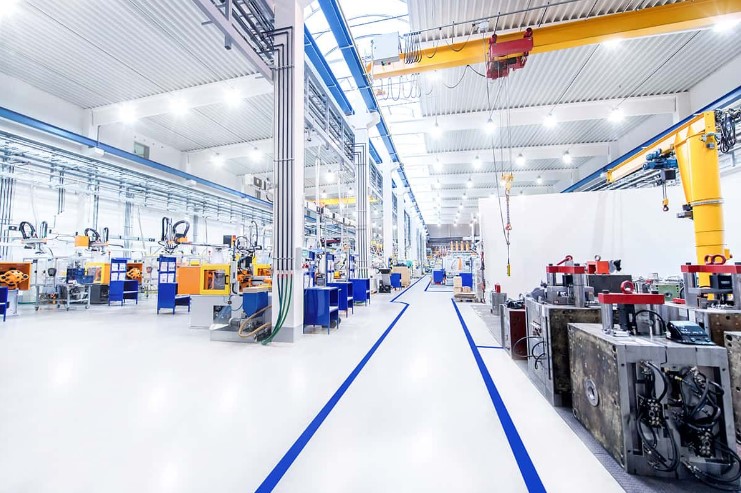
Plastic fabrication services are a crucial part of the manufacturing industry. They involve the creation of plastic products through a variety of processes such as injection molding, CNC machining, and vacuum forming. These services are essential for businesses that require customized plastic products for their operations. From custom plastic enclosures to signage and displays, plastic fabrication services can be used for a wide range of applications. In this blog post, we will cover everything you need to know about Plastic fabrication services by TK Fabrications, including the types of plastic used, and the benefits of using these services for your business needs.
Types of Plastic Used in Fabrication
A. Acrylic
Acrylics are a popular type of plastic used in fabrication, also known as polymethyl methacrylate (PMMA) or simply as “acrylic.” Acrylics are lightweight, strong, and offer a high degree of transparency that is similar to glass, making them an ideal material for many applications. They are also resistant to shattering, making them a safer option for high-impact or outdoor applications.
Acrylics are commonly used in signage, display cases, lighting fixtures, and other decorative applications due to their clarity and ability to be easily shaped and colored. They are also used in medical and scientific settings, where their transparency and resistance to UV radiation make them useful for applications such as lenses, protective barriers, and laboratory equipment.
B. HDPE
High-density polyethylene (HDPE) is a versatile and durable plastic used in fabrication for a wide range of applications due to its high strength-to-density ratio, impact resistance, and chemical resistance. HDPE is commonly used for outdoor applications such as pipes, tanks, and playground equipment due to its durability, and is also used for packaging materials such as bottles and containers for chemicals and hazardous materials due to its resistance to chemicals. HDPE can be formed through processes such as blow molding, extrusion, and injection molding.
C. PVC
Polyvinyl chloride (PVC) is a synthetic plastic polymer that is commonly used in fabrication due to its low cost, durability, and ease of processing. PVC is used for a variety of applications including construction, healthcare, and consumer products. Its properties can be modified by adding plasticizers and stabilizers to make it more flexible and resistant to UV radiation. PVC is commonly used for piping, roofing, flooring, and electrical cable insulation. PVC can be formed through processes such as extrusion, injection molding, and blow molding.
D. Other Plastic Types
In addition to acrylic, HDPE, and PVC, there are many other types of plastics that are used in fabrication services. Some of these plastics include:
- Polycarbonate: a clear, impact-resistant plastic used for applications such as lenses, screens, and safety glass.
- PET: a lightweight and strong plastic used for food and beverage packaging, and also for textile fibers.
- Nylon: a strong and durable plastic used for applications such as gears, bearings, and electronic components.
- Polystyrene: a rigid and brittle plastic used for applications such as packaging, disposable cups and plates, and insulation.
- ABS: a tough and rigid plastic used for applications such as toys, automotive parts, and luggage.
The selection of a specific plastic type for a given application depends on factors such as the required properties, the manufacturing process, and the cost. Plastic fabrication services can help determine the most appropriate plastic for a given application and ensure that the desired properties are achieved through proper fabrication techniques.
Processes Used in Plastic Fabrication Services
A. Injection Molding
Injection molding is a common process used in plastic fabrication services, particularly for large-scale production runs of plastic parts. In this process, molten plastic is injected into a mold under high pressure, where it cools and solidifies to form a specific shape. The mold is usually made of steel and consists of two halves, one that holds the cavity of the desired shape and another that holds the ejector pins and other features needed to release the part from the mold.
Injection molding allows for the creation of complex shapes with a high degree of accuracy and repeatability. The process is often automated and can produce large volumes of parts at a relatively low cost per unit. Injection molding is used to manufacture a wide range of products, from small and intricate components to large and complex structures.
The benefits of injection molding include:
- High production output and efficiency
- The ability to create complex shapes with tight tolerances
- Consistent and repeatable results
- The ability to use a wide range of plastic materials
- Low labor costs
Injection molding is a versatile and cost-effective process that is ideal for many plastic fabrication applications, including automotive parts, medical devices, and consumer products.
B. CNC Machining
CNC (computer numerical control) machining is another process used in plastic fabrication services. In this process, a computer-controlled machine is used to remove material from a block of plastic to create a specific shape or part. The CNC machine is programmed with precise instructions for cutting and shaping the plastic, and it uses a range of cutting tools to achieve the desired result.
CNC machining offers a high degree of precision and flexibility, allowing for the creation of complex shapes and parts with tight tolerances. The process is particularly useful for producing small to medium-sized batches of parts with a high degree of accuracy and consistency. CNC machining is often used in the production of prototypes and small to medium-scale production runs of parts.
The benefits of CNC machining include:
- High precision and accuracy
- The ability to produce complex shapes and parts with tight tolerances
- Flexibility in the range of plastic materials that can be used
- A wide range of finishes and surface textures can be achieved
- High efficiency and repeatability
CNC machining is a versatile and precise process that is ideal for many plastic fabrication applications, including medical and aerospace components, automotive parts, and consumer products.
C. Vacuum Forming
Vacuum forming is a process that involves heating a sheet of plastic until it becomes pliable, and then forming it over a mold using vacuum pressure. The vacuum pressure is applied to the heated plastic, which is drawn tightly around the mold to create a specific shape or part.
Vacuum forming is a versatile and cost-effective process that can be used to create a wide range of plastic parts and components. The process is particularly useful for producing large, low-cost parts in high volumes, and is often used in the manufacture of consumer products, automotive components, and industrial equipment.
The benefits of vacuum forming include:
- Cost-effective production of large parts
- Quick turnaround times
- The ability to produce a range of shapes and sizes
- High volume production capabilities
- Versatility in the types of plastic materials that can be used
Vacuum forming is a useful process for a variety of plastic fabrication applications, including the production of packaging materials, automotive parts, and medical devices. With its ability to produce high volumes of parts quickly and cost-effectively, vacuum forming is a popular choice for manufacturers in many industries.
D. Other Processes
- Overview of other plastic fabrication processes
- Explanation of each process and their applications in plastic fabrication services.
Benefits of Plastic Fabrication Services
A. Design Flexibility
Design Flexibility is one of the major benefits of plastic fabrication services. Due to the malleability of plastic, it can be molded into almost any shape or form. This allows for limitless design options, making it ideal for creating unique and complex designs that are difficult to produce with other materials.
Plastic fabrication services allow for a wide range of design options, including custom colors, finishes, textures, and patterns. This makes plastic an ideal choice for creating branded products, custom components, and unique packaging. With plastic fabrication services, designers have the freedom to explore new and innovative ideas without being limited by the constraints of traditional manufacturing methods.
In addition, plastic fabrication services offer design flexibility in terms of material selection. With a wide range of plastic materials available, designers can choose the best material for their specific application, based on factors such as strength, flexibility, chemical resistance, and UV stability.
B. Material Versatility
- Explanation of how different plastic types can be used in plastic fabrication services
- Advantages of material versatility in plastic fabrication
C. Cost-Effective
Plastic fabrication services are generally cost-effective and offer a more affordable alternative to other materials. Due to the fact that plastic can be molded and shaped more easily, the cost of fabrication is significantly lower than with other materials. This is especially true in high-volume production runs, where the cost per unit can be significantly reduced through the use of plastic fabrication.
Additionally, plastic fabrication can also help reduce material waste and scrap. In traditional manufacturing processes, excess material is often generated as a byproduct, resulting in increased costs and environmental impact. However, with plastic fabrication, the ability to mold and shape the material results in less material waste and lower production costs.
Furthermore, plastic fabrication services offer a longer lifespan than traditional materials, such as metal or wood. This makes it a cost-effective option for projects that require durability and longevity. As a result, businesses can enjoy long-term cost savings and an increased return on investment.
In conclusion, plastic fabrication services offer numerous benefits, including design flexibility, durability, and cost-effectiveness. With a variety of plastic types and fabrication processes available, businesses can find the right solution for their specific needs. By leveraging these benefits, businesses can improve their products, reduce costs, and increase their competitive advantage in the market.
D. Durability and Strength
- Explanation of the durability and strength of plastic materials
- Examples of plastic applications in industries that require high durability and strength
E. Aesthetics
- Explanation of how plastic fabrication services can create aesthetically pleasing products
- Examples of plastic applications in industries that require aesthetic appeal
F. Environmental Benefits
- Explanation of the environmental benefits of plastic fabrication services
- Examples of sustainable plastic materials and practices in plastic fabrication services.
Conclusion
Plastic fabrication services offer a wide range of benefits that make them an attractive option for various industries. The design flexibility, material versatility, cost-effectiveness, durability, and aesthetics of plastic fabrication make it a popular choice for many businesses. Additionally, the environmental benefits of sustainable plastic materials and practices add to the appeal of plastic fabrication services.
The future of plastic fabrication services looks bright, with potential advancements and trends on the horizon. As the demand for plastic products continues to grow, so does the need for plastic fabrication services. It is important to recognize the significance of plastic fabrication services in society and to consider their benefits when seeking out fabrication options.
In light of these benefits, we encourage readers to consider plastic fabrication services for their specific needs. Whether it be for product design, manufacturing, or prototyping, plastic fabrication services offer a range of options for businesses of all types.