The Engineer – Comment: 3D printing next generation electrical machines


Additive manufacturing processes capable to develop future era power dense electrical machines will be a critical plank in our press for internet zero writes Dr Nick Simpson.
Electrical devices are interesting as they are equipped to convert electrical electrical power into mechanical electricity and again once again. In electrical motor vehicles, for illustration, this bi-directional conversion is exploited to present traction while driving, and regeneration even though braking.
This regeneration lets the kinetic electricity of the moving automobile to be transformed back into usable electrical power and saved in the battery, relatively than remaining squandered as warmth, as with traditional mechanical friction brakes.
The capacity to efficiently transform vitality between electrical and mechanical domains places electrical equipment at the heart of ongoing electrification attempts across the automotive, aerospace, industrial and strength sectors, in pursuit of our Carbon Internet Zero 2050 targets.
The United kingdom Aerospace Engineering Institute (ATI) and Superior Propulsion Centre (APC) who signify the upcoming technological innovation demands of the aerospace and automotive sectors respectively, demand electrical machine electricity-densities of involving 9 and 25 kW/kg by 2035, in stark distinction to the 2 to 5 kW/kg accessible nowadays even when making use of point out-of-the artwork lasting magnet supplies (this kind of as NdFeB), electrical steels (this kind of as CoFe) and large-functionality electrically insulated copper windings.
Regrettably, the energy conversion system among the electrical and mechanical domains is not 100{64d42ef84185fe650eef13e078a399812999bbd8b8ee84343ab535e62a252847} productive. Some energy is “lost” since it is transformed into undesirable types this kind of as sound, vibration and, predominantly, warmth.
Heat is created by mechanical friction in the bearings, hysteresis and eddy existing effects in the electrical steel and magnets, and from Joule and eddy current results in the winding conductors. Of these, the windings are usually the dominant supply of heat. This boosts the temperature of parts, with the temperature limit commonly imposed by the elements made use of for electrical insulation of the conductors.
When developing an electrical machine for substantial electrical power-density, we have to harmony the ability ranking, mass and quantity with the warmth produced and the ensuing temperature increase – becoming mindful not to exceed the style limit. It follows that the ability-density could be enhanced if we cut down the heat generated by the winding, enhance the thermal management to awesome the winding a lot more proficiently and/or raise the conductor electrical insulation temperature score.
Conventional windings are fashioned from cylindrical or rectangular cross-section conductors made by wire drawing procedures 1st documented as much back as the 12th century by Theophilus. Bundles of conductors can be employed to mitigate pores and skin result or cautiously transposed to form Litz style windings to harmony strand currents and minimize in general decline. The minimal vary of cross-sectional designs available and necessity to use a single conductor variety throughout a winding represent limitations to improved effectiveness.
Windings are ordinarily cooled by way of a liquid cooling jacked shrink-equipped to the stator, the place the heat generated in the conductors will have to traverse the electrical insulation technique, electrical metal, and quite a few thermally weak substance interfaces, before reaching the fluid. To boost this, spray cooling jets can be educated on the windings instantly to increase heat transfer at the price of complexity.
Conductor electrical insulation coatings are usually natural and organic polymers thanks to their substantial dielectric power, mechanical adaptability and toughness, which is preferably suited to the often arduous mechanical winding procedures used in manufacture. Nonetheless, higher temperature scores of 180 – 240oC position definitive limits on scorching-spot temperatures and preclude use in extreme temperature environments.

The adoption of steel AM processes can at the same time make it possible for the three style and design aims of lowering produced heat, bettering thermal administration, and boosting the electrical insulation temperature limit to be met.



An alternate to typical producing procedures is to adopt metal Additive Producing (AM) in which powdered substance or feedstock is selectively bonded in a succession of 2D layers to incrementally variety a 3D portion.
To date, copper, copper alloy and aluminium alloy windings have leveraged AM – or extra specially the LBPF process – with many positive aspects demonstrated. A person of the key rewards is the geometric liberty of the AM course of action. Not only does this allow for each individual conductor to be optimally formed but enables specific loss reduction approaches to be utilized. For illustration, conductors at the starting of a winding can be good and then transition to stranded, transposed bundles. That’s why, the most advantageous conductor sort and topology can be used in just about every part of the winding.
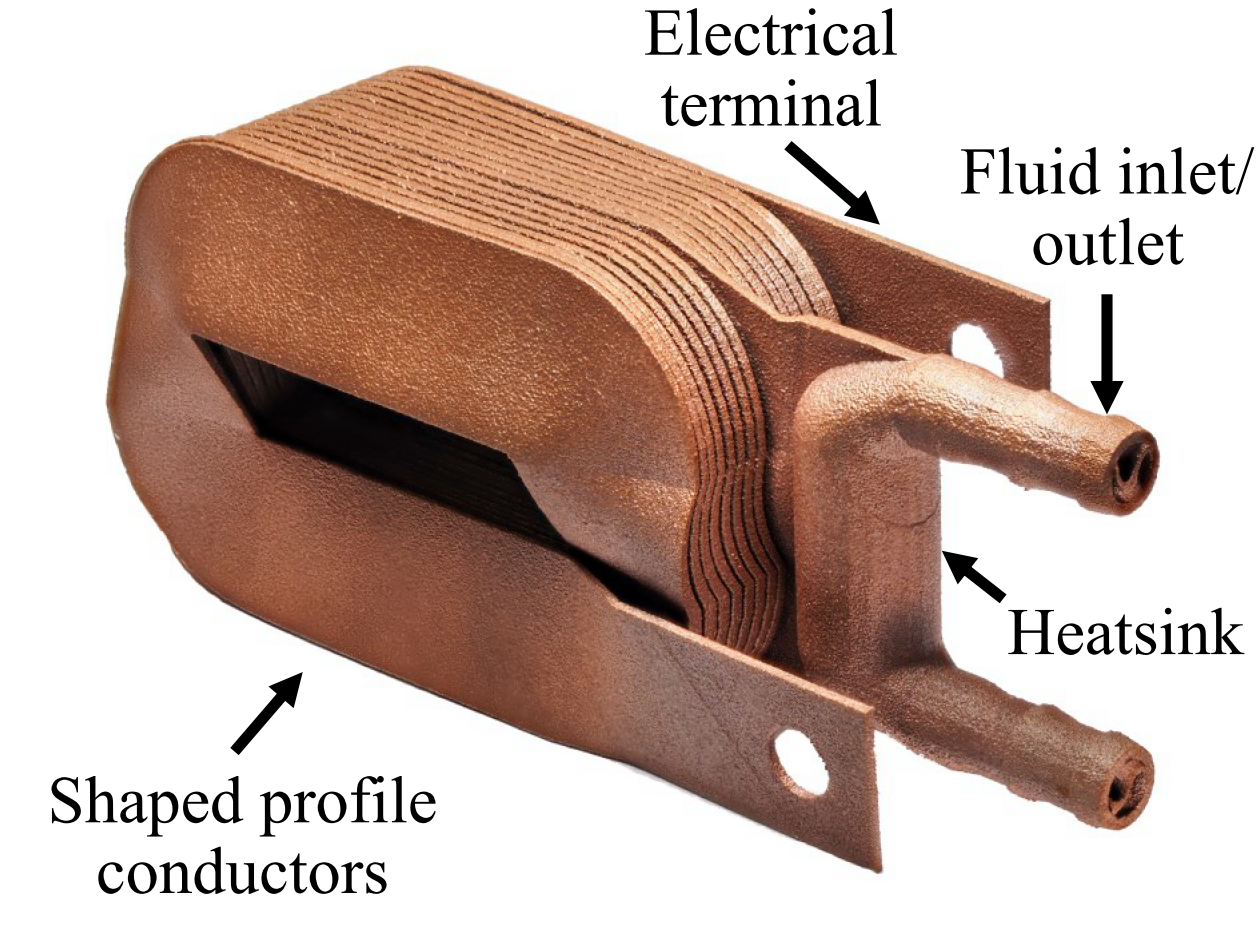
– Graphic: Dr. Nick Simpson, Electrical Power Administration Group (EEMG), College of Bristol and John Robinson and Dr. Arun Arjunan, Additive Producing of Functional Products (AMFM), University of Wolverhampton
A even further crucial benefit is the probability of new cooling strategies. For example, liquid cooling channels can be strategically embedded into conductors, or the stop-windings sculpted, to minimise volume and maximise warmth transfer. Complex lattices and periodic infill constructions can be used to form powerful heat exchangers to cool conductors without having encroaching on the conductive cross-portion.
Using the AM approach, windings are effectively made in their wound condition, eradicating the have to have for insulation coatings to withstand substantial mechanical hundreds. Hence, option significant-temperature products this kind of as ceramics could be adopted to deal with thermal limitations.
In essence, the adoption of steel AM processes can simultaneously permit the three structure aims of lessening generated warmth, increasing thermal administration, and boosting the electrical insulation temperature limit to be fulfilled. As these, phase changes in achievable electric power-density could be realised, taking us nearer to the 9 – 25 kW/kg targets in pursuit of Carbon Net Zero 2050.
Dr. Nick Simpson is a Senior Lecturer and UKRI Future Leaders Fellow at the College of Bristol wherever he started The Electrical Equipment Will work targeted on bringing Additive Producing to the style and design of higher general performance electrical equipment.
If you’d like to listen to a lot more from – and community with – AM leaders, visionaries and innovators, be sure to be a part of us in Nottingham at this year’s Additive Intercontinental summit, 13-14th July. Visit https://www.additiveinternational.com/ for far more facts.